Enhancing Goods-To-Person with Pouch Technology
12th March 2025
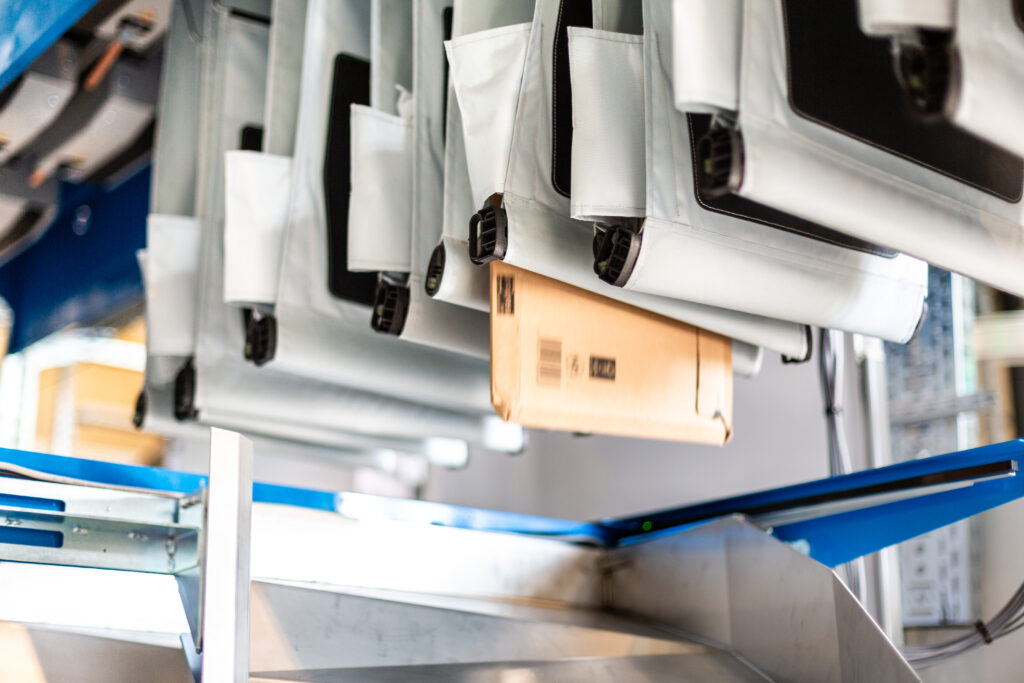
The explosion of e-commerce has fundamentally changed the operations within warehousing and distribution, and fulfillment centers. Previously, these facilities handled large, bulk orders destined for retail stores, a process that was predictable and could be planned. However, the rise of online shopping has introduced a more complex sortation scenario. Goods to Person (GtP) involves the distribution and fulfillment of orders to numerous individual consumers who may order just one or two items at a time.
The shift to GtP has created significant challenges, including the need for sortation facilities to perform tasks traditionally managed by retailers, such as distinguishing between item sizes and colors for B2C orders. Another area that has become more challenging is the management of returns. Return rates can reach as high as 60% in the e-commerce sector. Handling these returns (reverse logistics) involves multiple steps, including quality checks, relabeling, and repacking, all of which add to the complexity and cost of operations.
A basic GtP system can be configured as an inventory buffer, or a pick system, or both. No matter what the setup, most of the system’s capacity will still be allocated for basic warehousing needs like receiving, storing and picking. Post picking processes like ship order consolidation, sortation, sequencing and shipping require advanced configuration of the GtP or an additional high-capacity subsystem that can interface with the GtP. This is where a pouch system comes into play. It acts as a consolidation buffer system that will be complimentary to the existing GtP setup without any need for complicated reconfiguration.
Pouch system solutions
Essentially, a pouch sorter comprises a conveyance system of hanging pouches that carry products along a rail. Pouch systems are designed to transport a wide range of items, including garments, shoes, books, and other merchandise, offering high flexibility. Pouch technology is very scalable, modular and can be installed in unused overhead space offering the ability to buffer, sort, and sequence; automating the order handling and returns processes.
Pouch sortation systems facilitate processes such as post picking sortation, order batching & sortation, and intermediate storage handling of returned items. A typical application of pouch systems would be to efficiently handle throughput, temporary inventory buffer and order consolidation regardless of whether an order consists of two items or ten. Various sequencing challenges can be easily tackled by a pouch system. For example, ensuring that the most fragile or delicate items are sorted last, so that they are packed last in order to avoid damage. Thus, a pouch system can play a pivotal role in simplifying the returns process by reducing costly touchpoints and streamlining the overall process by establishing traceability and control to improve overall process efficiency.
Reducing touch points
Pouch system technology is constantly evolving. Beumer Group has recently added an innovative AutoDrop feature to its BG Pouch System to enable flexible and reliable automatic packing lines. In this system, pouches are unloaded from the bottom using a pioneering nickel-titanium alloy first used in the medical industry. This metal alloy has shape memory and will contract substantially when electric power is applied. When the power is withdrawn, the alloy returns to its original shape. Each mechanism has the capability for one million opening cycles without any deviation.
AutoDrop uses these characteristics to open the pouch automatically at the unloading point, enabling GtP operations to eliminate manual handling during unloading. This saves time at the unloading stations and reduces order lead time. The BEUMER Group Pouch System with AutoDrop can process approximately 10,000 pieces per line per hour. Combining multiple, adjustable drop point positions in one single drop line enhances flexibility to accommodate different unloading needs, while significantly reducing the physical footprint within the distribution facility.
This AutoDrop feature enables reduced touch operation for the entire pouch handling process, as well as offering customers substantial benefits in terms of reducing order lead time and saving valuable floor space.
Delivering digitization
As the GtP industry continues to innovate, the adoption of data-driven and software-based solutions will be key to creating the warehouse of the future.
Acting as the cornerstone of the Pouch System is the warehouse management software (WMS). The Pouch WMS supports digitization of the warehousing process from inventory management to ship order consolidation. This digital footprint provides the user with enhanced tracking, traceability and control at each step of the process. Digitization options such as this create the possibility of process optimization for efficiency and thus, enhancement of the entire fulfillment experience.
Pouch as an enhancement to GtP
Making a business case for deploying a new materials handling system will be different for each GtP operation, depending on your priorities and business needs. Factors include the type of building and available footprint, the type of products or items and their sizes, and the level of returns to be managed, along with your labor requirements and CAPEX and OPEX considerations.
However, the reasons to deploy a pouch system are compelling. Pouch systems are easily retrofitted into existing base GtP operations. They provide mid- to short-term storage, acting as a ship buffer with automated sortation and sequencing capabilities. Pouch systems can also help optimize the reverse logistics process. Scalable and modular pouch systems can grow as the e-commerce market expands. Their ability to integrate with other systems facilitates digitization, giving GtP businesses greater data insights that will further enhance productivity.
similar news